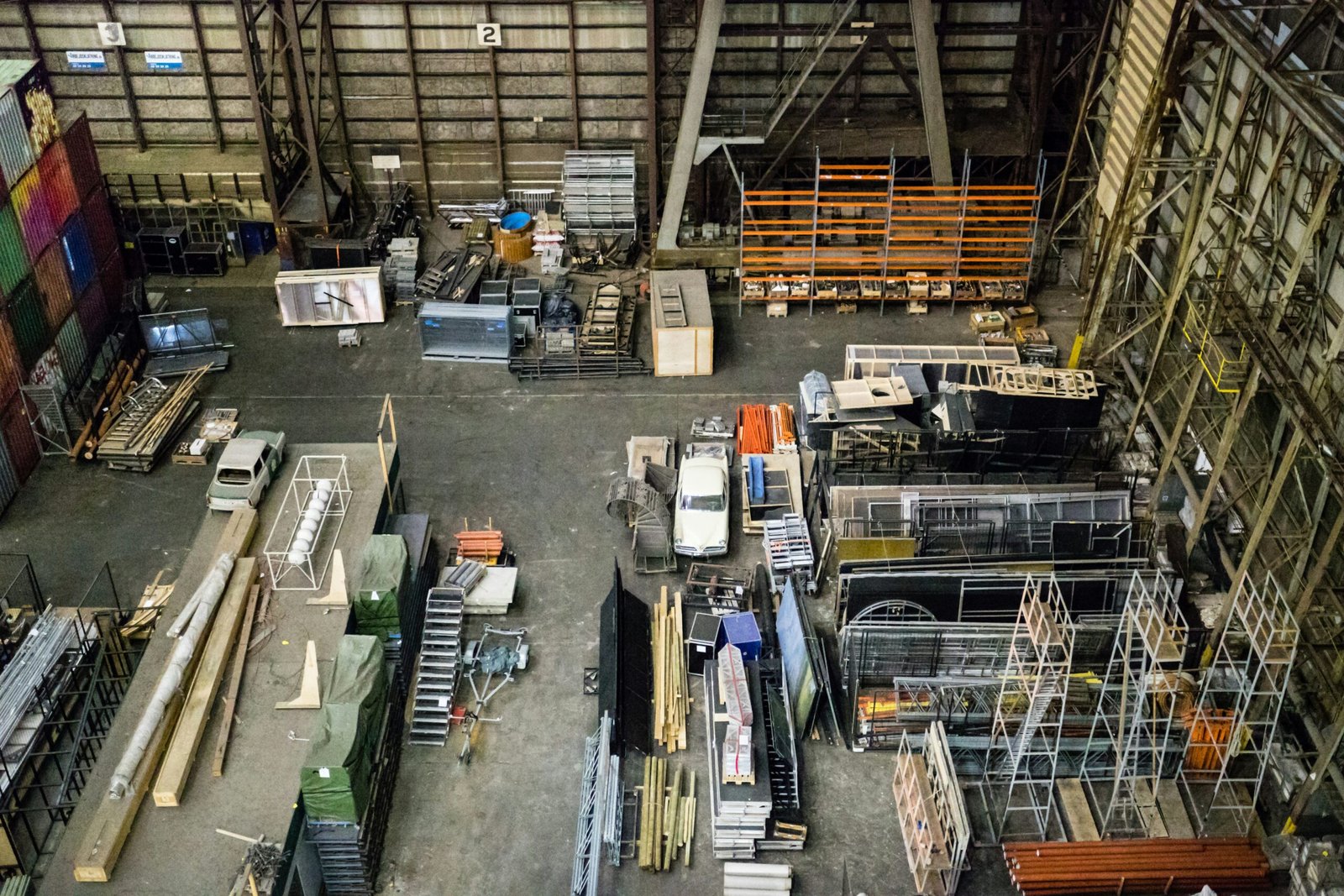
What is Batch Manufacturing Records: A Comprehensive Guide
Introduction to Batch Manufacturing Records (BMR)
Batch Manufacturing Records (BMR) are crucial documents in the manufacturing sector, meticulously detailing the production process for each batch of products. These records serve as a comprehensive guide, from raw material procurement to the final product’s packaging. The primary purpose of a BMR is to ensure consistency, traceability, and compliance with industry standards and regulatory requirements.
The significance of BMRs in the manufacturing industry cannot be overstated. They provide a structured and systematic approach to documenting the entire manufacturing process, thereby minimizing errors and ensuring product quality and safety. Moreover, BMRs play a pivotal role in facilitating audits and inspections by regulatory bodies, as they offer transparent and verifiable records of manufacturing activities.
Various industries rely heavily on Batch Manufacturing Records to maintain high production standards. In the pharmaceutical industry, BMRs are indispensable for tracking the production of medications, ensuring that each batch meets stringent quality and safety standards. Similarly, the food production sector uses BMRs to document the manufacturing process of consumables, guaranteeing that products are safe for consumption and free from contaminants. The chemical manufacturing industry also utilizes BMRs to maintain consistency and safety in the production of chemicals, thus preventing hazardous incidents and ensuring regulatory compliance.
Understanding the purpose and importance of BMRs is essential for professionals in these industries. These records serve as a testament to a company’s commitment to quality and safety and as a critical tool for continuous improvement in manufacturing processes. By meticulously documenting every aspect of production, BMRs help companies identify and rectify issues, optimize processes, and enhance overall efficiency.
Components of a Batch Manufacturing Record
A Batch Manufacturing Record (BMR) is a critical document in the pharmaceutical and manufacturing industries. It encapsulates the entire production history of a batch of products and serves as a cornerstone for ensuring product quality and regulatory compliance. The components of a BMR are meticulously outlined to provide a comprehensive account of the manufacturing process. These components include raw material details, process parameters, equipment used, and personnel involved, each playing a vital role in the overall integrity of the production process.
Firstly, raw material details are fundamental. This section records the specific materials used in the batch, including their source, lot numbers, and quality control test results. Accurate documentation of raw materials is essential to trace any quality issues back to their origin and ensure the final product’s consistency and safety.
Secondly, process parameters are documented to capture the precise conditions under which the batch was manufactured. This includes temperatures, pressures, mixing times, and other critical variables. Manufacturers can ensure that each batch is produced under optimal conditions by meticulously controlling and recording these parameters, thereby maintaining product consistency and efficacy.
Equipment used in the manufacturing process is another crucial component of the BMR. This section details the machinery and tools, including their calibration and maintenance records. Equipment documentation helps to guarantee that all devices function correctly and are suitable for production tasks, reducing the likelihood of equipment-related errors that could compromise product quality.
The BMR also records the personnel involved in the manufacturing process, including the names and roles of operators, supervisors, and quality control staff. Documenting personnel ensures accountability and provides a traceable record of who performed each task. This is particularly important for identifying and addressing any human errors that may occur during production.
Overall, each component of a Batch Manufacturing Record is integral to producing high-quality, compliant products. Meticulous documentation in these areas facilitates regulatory compliance and enhances the traceability and reliability of the manufacturing process.
The Role of BMR in Quality Control
Batch Manufacturing Records (BMRs) are indispensable tools in quality control within manufacturing processes. These comprehensive documents meticulously capture each step of the production cycle, ensuring that every batch is produced consistently according to predefined standards. The systematic documentation inherent in BMRs is a critical mechanism for maintaining product uniformity, detecting deviations, and upholding stringent quality benchmarks.
One of the primary functions of a BMR is to ensure that each stage of the manufacturing process is recorded with precision. This includes raw material selection, equipment calibration, process parameters, and environmental conditions. By detailing these aspects, BMRs provide a transparent trail that can be reviewed and audited to confirm that every batch adheres to the established specifications. This level of documentation is essential for identifying any anomalies that may arise during production, enabling manufacturers to address and rectify issues promptly.
Quality control checks integrated into BMRs can cover a wide range of aspects. For instance, in pharmaceutical manufacturing, BMRs might include checks for correct ingredient measurements, mixing times, and temperature controls. These checks verify that each batch meets the necessary criteria before proceeding to the next production phase. Similarly, in the food industry, BMRs can document critical points such as cooking temperatures and times, ingredient sourcing, and packaging integrity.
By embedding quality control measures directly into the BMR, manufacturers can ensure a continuous monitoring process that highlights deviations almost in real time. This proactive approach enhances the final product’s reliability and fosters compliance with industry regulations and standards. Furthermore, the comprehensive nature of BMRs facilitates root cause analysis in the event of product recalls or quality complaints, thereby contributing to continuous improvement in manufacturing practices.
Regulatory Requirements and Compliance
Batch Manufacturing Records (BMRs) ensure that pharmaceutical products meet stringent quality standards and regulatory requirements. Regulatory bodies such as the U.S. Food and Drug Administration (FDA), the European Medicines Agency (EMA), and other international authorities have established comprehensive guidelines to govern BMRs’ creation, maintenance, and review.
Under 21 CFR Part 211, the FDA stipulates that BMRs must document all aspects of production, including raw material usage, equipment calibration, and process parameters. These records must be accurate, contemporary, and complete to ensure that each batch of products meets the predefined quality criteria. The FDA also requires that BMRs be readily accessible for inspection, emphasizing the importance of transparency and traceability in pharmaceutical manufacturing.
Similarly, the EMA has laid out detailed requirements in its EudraLex Volume 4 guidelines, which align closely with Good Manufacturing Practice (GMP) principles. These guidelines mandate that BMRs include detailed instructions and records of each stage of the manufacturing process, ensuring consistency and quality across all batches. The EMA also requires that deviations and corrective actions be thoroughly documented and investigated to prevent recurrence.
International standards, such as those from the International Council for Harmonisation (ICH), further complement these regulatory frameworks by providing harmonized technical guidelines for the pharmaceutical industry. Compliance with these standards facilitates international trade and ensures that products meet the highest safety and efficacy standards.
Adhering to these regulatory requirements is essential for pharmaceutical companies to avoid legal issues, product recalls, and potential consumer harm. Non-compliance can result in significant financial penalties, reputation damage, and consumer trust loss. Therefore, maintaining meticulous and compliant BMRs is not merely a regulatory obligation but a critical component of quality assurance in the pharmaceutical industry.
Best Practices for Creating and Maintaining BMRs
Effective batch manufacturing records (BMRs) are central to maintaining the integrity and consistency of production processes. To ensure reliability, it is essential to adhere to best practices in creating and maintaining these records. Accurate data entry is the cornerstone of any robust BMR system. Every detail must be meticulously documented, from raw material specifications to individual process steps. This ensures traceability and accountability throughout the manufacturing process, reducing the risk of errors or deviations.
Maintaining regular updates is another critical aspect. BMRs should reflect real-time changes and modifications in the production processes. This can involve updating standard operating procedures (SOPs), adjusting formulations, or recording equipment maintenance activities. Regularly updated records help identify and address issues promptly, ensuring continuous process improvement and compliance with regulatory standards.
The secure storage of BMRs is paramount to protecting sensitive production data. Whether in physical or digital format, BMRs must be stored in a manner that prevents unauthorized access, loss, or damage. Implementing strict access controls and using secure storage solutions can safeguard this vital information. For physical records, this might mean using locked cabinets in controlled environments. Employing encrypted databases and secure cloud storage solutions can offer protection and ease of access to digital records.
Periodic reviews are essential to maintaining the relevance and accuracy of BMRs. Conducting scheduled audits and reviews helps ensure that the records are complete, accurate, and up-to-date. This practice also facilitates compliance with industry regulations and standards, providing a clear, documented manufacturing process history.
Incorporating digital solutions can significantly streamline BMR management. Advanced software tools and platforms can automate data entry, updates, and storage, reducing manual errors and saving time. Digital BMR systems can provide real-time analytics and reporting, enhancing decision-making and operational efficiency. Leveraging BMR management technology can improve accuracy, security, and compliance.
Common Challenges and How to Overcome Them
Creating and maintaining Batch Manufacturing Records (BMRs) involves several challenges that can impact their accuracy and reliability. One of the most prevalent issues is human error. Manual data entry, misinterpretation of protocols, and oversight can lead to inaccuracies in BMRs. To mitigate this, implementing robust training programs for staff is crucial. Regular training sessions ensure that employees are well-versed in standard operating procedures (SOPs) and understand the importance of precision in recording data.
Another significant challenge is maintaining data integrity. BMRs must be tamper-proof and reflect accurate information throughout the manufacturing process. Utilizing electronic batch records (EBRs) can enhance data integrity. EBRs provide automated data capture, reducing the risk of manual entry errors and ensuring real-time data synchronization. Additionally, incorporating audit trails within EBR systems can help track any modifications, providing a transparent history of all changes made to the records.
Regulatory changes also pose a challenge in maintaining compliant BMRs. The pharmaceutical and manufacturing industries are subject to stringent regulations that frequently evolve. Staying updated with these regulatory changes is essential to ensure BMR compliance. Establishing a dedicated regulatory affairs team that monitors and interprets new guidelines can help organizations adapt their BMR practices accordingly. Additionally, leveraging regulatory compliance software can facilitate the timely update of records and ensure adherence to the latest standards.
Lastly, integrating quality control measures throughout the manufacturing process can significantly enhance the reliability of BMRs. Regular internal and external audits can identify discrepancies early and ensure corrective actions are taken promptly. Implementing a robust quality management system (QMS) can further support continuous improvement and uphold the integrity of BMRs.
By addressing these common challenges with proactive strategies, organizations can ensure that their Batch Manufacturing Records remain accurate, reliable, and compliant with regulatory requirements.
Case Studies: Successful Implementation of BMRs
Implementing a Batch Manufacturing Record (BMR) system can be a transformative step for companies in the pharmaceutical and manufacturing sectors. Several organizations have navigated this journey successfully, overcoming challenges and reaping substantial benefits. These real-life case studies illustrate the practical application of BMR systems, providing valuable insights for those looking to enhance their processes.
One notable example is a mid-sized pharmaceutical company that faced significant compliance issues due to inconsistent documentation practices. Their manual record-keeping could have been more accurate, leading to regulatory challenges and production delays. The company implemented an electronic BMR system to streamline its documentation process. Doing so significantly reduced human error, improved data accuracy, and ensured real-time compliance with regulatory standards. The transition was challenging; initial resistance from the staff and the need for comprehensive training were major hurdles. However, the company successfully adopted the new system with effective change management strategies and robust training programs. The result was a 30% reduction in compliance-related issues and a 20% increase in production efficiency.
Another case involves a large-scale food manufacturing company that needed help with traceability and inventory management. Their paper-based BMRs could have been more convenient, often leading to product recalls and quality control process delays. By moving to a digital BMR system, the company enhanced its traceability capabilities, allowing for faster and more accurate identification of issues within the supply chain. This change improved their response time during recalls and bolstered their overall quality assurance framework. The implementation process included upgrading their IT infrastructure and conducting extensive staff training. Post-implementation, the company reported a significant improvement in inventory management and a 25% decrease in recall times, enhancing its market reputation.
These case studies underscore the transformative potential of BMR systems. Companies can achieve significant operational improvements by addressing specific challenges and adopting tailored solutions. These organizations’ experiences highlight the importance of thorough planning, effective training, and robust change management in the successful implementation of BMR systems.
Future Trends in Batch Manufacturing Records
As the manufacturing sector evolves, Batch Manufacturing Records (BMRs) are also undergoing significant transformations. Emerging technologies such as blockchain, Artificial Intelligence (AI), and the Internet of Things (IoT) are at the forefront of this evolution, promising to revolutionize how BMRs are created, maintained, and utilized.
Blockchain technology offers a decentralized and immutable ledger system that ensures the integrity and traceability of batch records. By leveraging blockchain, manufacturers can create a transparent and tamper-proof system for recording every manufacturing process step. This enhances data security and facilitates regulatory compliance by providing a reliable audit trail that can be accessed in real-time.
Artificial Intelligence (AI) is another game-changer in the realm of BMRs. AI algorithms can analyze vast amounts of data to identify patterns and anomalies that may indicate potential issues in the manufacturing process. Predictive analytics powered by AI can help address problems preemptively, reducing downtime and increasing overall efficiency. Additionally, AI can automate repetitive tasks such as data entry and validation, freeing up human resources for more strategic activities.
The Internet of Things (IoT) brings a new dimension to BMRs by enabling real-time data collection from various sensors and devices on the manufacturing floor. IoT can provide granular visibility into the production process, allowing for continuous monitoring and immediate corrective actions if deviations are detected. This real-time insight improves product quality and enhances the accuracy and comprehensiveness of batch records.
These technological advancements collectively contribute to a more efficient, accurate, and compliant manufacturing process. By integrating blockchain, AI, and IoT into BMRs, manufacturers can ensure a higher standard of operational excellence and regulatory adherence, setting new benchmarks for the industry.